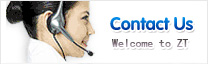
![]() ![]() ![]() ![]() ![]() ![]() ![]() ![]() |
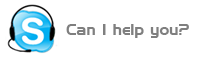
Historical Background on Bricks and Brickmaking-II
When dry the bricks need firing, the simplest method to do this is with a large pile of bricks and fuel mixed together and ignited. The main problem with this is there is little control over the final temperature. Usually some bricks were over heated and distorted, whilst others were left under fired and were too soft for use.
Most sites developed with some form of permanent kiln, the most basic of these are the up draught kilns. The most basic was the kiln which was basically four walls with fire holes in the sides which lead under a perforated floor onto which the bricks were stacked. The heat passed up through the bricks and out of the top of the kiln. There are a large number of variations on this with baffles and various flue systems which control the flow of the gases and heat through the kiln and the temperature within the kiln. The development of these kilns eventually lead to the downdraught kilns were the heat is pulled through the bricks from the top due to a draught from a large chimney.
Most of the smaller brickyards had single fire kilns. The kilns were loaded with bricks, the kilns were lit and the bricks were burnt, the kiln was then allowed to cool before the bricks could be removed. This cycle usually took about a week. The larger brickworks built continuous kilns based on the Hoffmann design. These had a series of interlinked chambers usually of an oval design. Wet bricks were stacked in one chamber and warm flue gases from a previous chamber, which was been fired, were drawn over them to dry them. The firing point was slowly moved around the series of chambers by adding fuel to the chambers usually from above. This allowed for the continuous burning of bricks.
In Zhengtai, our biggest success comes from the customers' success. We believe in providing not only the quality machine, but also to work closely with our customers from the beginning of their project to the end. For many years, Zhengtai has aimed to form a very helpful service team so that at anytime in anywhere our customers can benefit from it.
