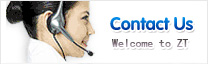
![]() ![]() ![]() ![]() ![]() ![]() ![]() ![]() |
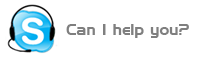
How Clay Bricks Were Made from the Mid 1800s to the Early 1900s in USA-Ⅰ
1. PREPARING THE INGREDIENTS
The main ingredients were clay and sand or shale. The clay was dug from the shore or from under bodies of water (such as the Hudson River). Beach sand mixed in very well and improved the quality of the brick, but in some places along the Hudson there was up to 12 inches of oyster shells lying on top-these had to be removed, as the chemical reaction from the slaked lime would crack the brick. The clay had to be dredged in early spring or late fall to allow time for seasoning and all the water had to drain off. Next, the clay was screened to remove rocks and the shale and clay were ground into powder by a crusher and stored.
Here a team of mules and horses is being used to haul a two-wheeled scraper to a platform where the clay powder was dumped into small, side-dumping railroad carts called "dinkies" which were pulled by cables or small locomotives.
In the Pug Mill, water was added to the powder and the clay and sand mixture was soaked, stirred and kneaded with large augers or wooden paddles until doughy. This step was called tempering or pugging and was the hardest work of all. In the mid-1800's horse driven pug mills were invented. The clay was removed from the soaking pit or pug mill by a temperer who delivered it to the moulding area.
2. MOULDING
Before the invention of steam-driven machines, bricks were moulded by hand. A great description of this is on the web site Ricks-Bricks: "The assistant brick moulder was called the "clot" moulder and he would prepare a lump of clay and give it to the brick moulder. The brick moulder was the key to the operation and he was the head of the team. He would stand at the moulding table for twelve to fourteen hours a day and with the help of his assistants could make 3500 to 5000 bricks in a day. He would take the clot of clay, roll it in sand and "dash" it into the sanded mould. The clay was pressed into the mould with the hands and the excess clay removed from the top of the mould with a strike, which was a flat stick that had been soaking in water. This excess clay was returned to the clot moulder to be reformed. Sand was used to prevent the clay from sticking to the mould."
"Single, double, four or six brick moulds were used. The single brick mould had an advantage in that a child could carry it to the drying area. Beechwood was the preferred material for the mould for it was claimed that the clay would not stick to it. The top of the mould was laminated with iron to prevent wear. The brick slid easily out of the mould because it was sanded and these bricks are referred to as 'sand struck bricks.' The process was also referred to as slop moulding."
"The next person on the team was called an off-bearer. He would walk up to the moulding table, remove the filled mould and take it to a drying area on a pallet or barrow where it would be placed on a level bed of sand. He would then return the mould to the table and wet and sand it to receive the next brick."
Over the years a few rudimentary tools were introduced to help streamline production and in 1830, Nathaniel Adams of Newburgh and Cornwall, NY, invented a moulding machine. However this required human or animal labor to operate.
The real break-through came in 1852, when a steam-powered machine was developed by Richard VerValen. Other early brick-making machines like this one, patented in 1863 by Cyrus Chambers of Philadelphia, used stiff mud which was forced out in long ribbons on a conveyor belt, transferred to moulds and cut by a revolving cutter. As time progressed, up to 25 brick could be cut at a time. The brick were then stamped with the appropriate name or design.
